Blade rupture-prevention technology
In turbomachines of steam turbine, flue gas turbine and hydroturbine, fractures and even ruptures of blades are common problems. Damping ring developed for controlling the vibration force amplitude may extend the service life of blades, and has been applied to the turbomachines of multiple steam turbines.
In turbomachines of steam turbine, flue gas turbine and hydroturbine, fractures and even ruptures of blades are common problems. Damping ring developed for controlling the vibration force amplitude may extend the service life of blades, and has been applied to the turbomachines of multiple steam turbines.
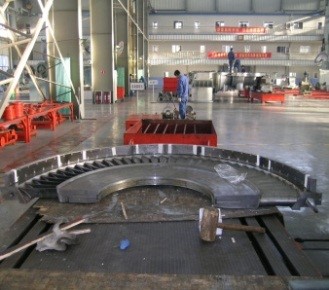
Engineering application of blade rupture preventing technology
High-performance sealing technology
At present, the operation efficiency of generating sets of many steam turbines is relatively low in China, and the waste of resources and economic loss are relatively big as a result. The technology settles the problems of steam turbine axle-end air leakage and water-bearing lubricant of steam turbine, improves the efficiency of steam turbine, and ensures safe operation of the regulating system and bearings.
At present, the operation efficiency of generating sets of many steam turbines is relatively low in China, and the waste of resources and economic loss are relatively big as a result. The technology settles the problems of steam turbine axle-end air leakage and water-bearing lubricant of steam turbine, improves the efficiency of steam turbine, and ensures safe operation of the regulating system and bearings.
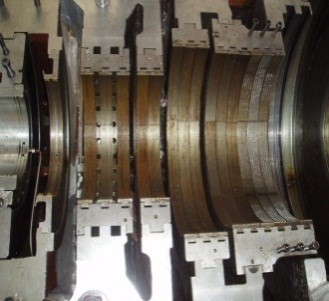
High-performance sealing technology
Adjustable automatic tracking and composite honeycomb seal
The new technology is mainly applied to axle-end oil seal of electric motor. The sealing device integrates the new-type high-efficient oil seal technology with honeycomb seal, solved the safety problems that lubricant may be absorbed into the electric motor and soak coils.
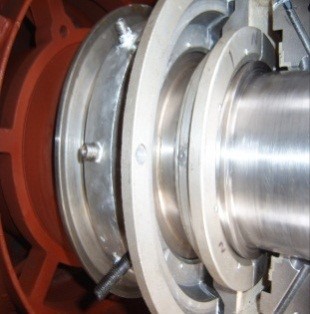
Composite honeycomb oil seal
Pipeline vibration damping technology
The technology may inhibit fatigue fracture of pipeline by installing a vibration damping device at a proper location without changing the original pipeline layout and thus extend the service life of pipelines. It's applicable to pipelines of reciprocating and centrifugal compressors, heat exchangers, air cooler collecting duct and other pipelines of petrochemical systems.
The technology may inhibit fatigue fracture of pipeline by installing a vibration damping device at a proper location without changing the original pipeline layout and thus extend the service life of pipelines. It's applicable to pipelines of reciprocating and centrifugal compressors, heat exchangers, air cooler collecting duct and other pipelines of petrochemical systems.
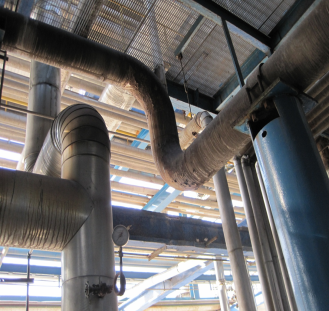
Pipeline damping